Features | Endurable and Long Lasting |
Material | C11000 copper foil, copper content ≥ 99.95% |
Electrical conductivity resistivity | ≤0.0012Ω/m |
Current capacity per unit area | 4A |
pressure drop | 3MV |
tensile strength | 240MPa |
twisting strength | 150MPa |
applications | commonly used as the flexible expansion joints for connecting the bus bars |
Section area | 10-500sqmm |
Packaging Details | standard thick carton |
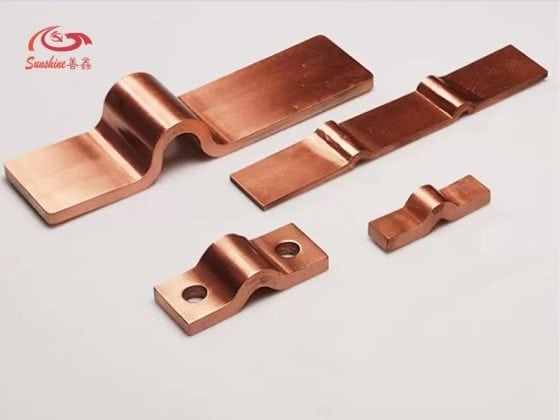
Brief introduction about no plating flexible copper foil laminated connector
No plating flexible copper foil laminated connector consists of C11000 copper foils, the both ends of which are press-welded together. The welding process is also called molecular diffusion welding which makes the lamination pressed and heated with each other, and then the contact area is shaped.
Single Foil Thickness:
- 0.03mm
- 0.05mm
- 0.10mm (standard)
- 0.20mm
- 0.30mm
- 0.40mm
The production process of no plating flexible copper foil laminated connector
The no plating flexible copper foil laminated connector is formed by two technologies. The first is to press the 0.05mm – 0.5mm thick copper foil laminate together partly , then adopt macromolecule diffusion welding technology. Finally, it is formed by argon welding with high current heating.
The second is to press 0.05mm – 0.5mm thick copper foil together, using silver based brazing material and flat copper block butt welding forming.
Each copper strip of the flexible copper foil laminated connectors with ferrules is cut by CNC punching and cutting machine tools. This can ensure that the difference between each piece of copper strip is balanced, the accuracy can reach 0.0001mm, and there is no extrusion between each piece due to uneven feeding, fully ensure that the expansion of soft connection is not limited.
The drawing of no plating flexible copper foil laminated connector
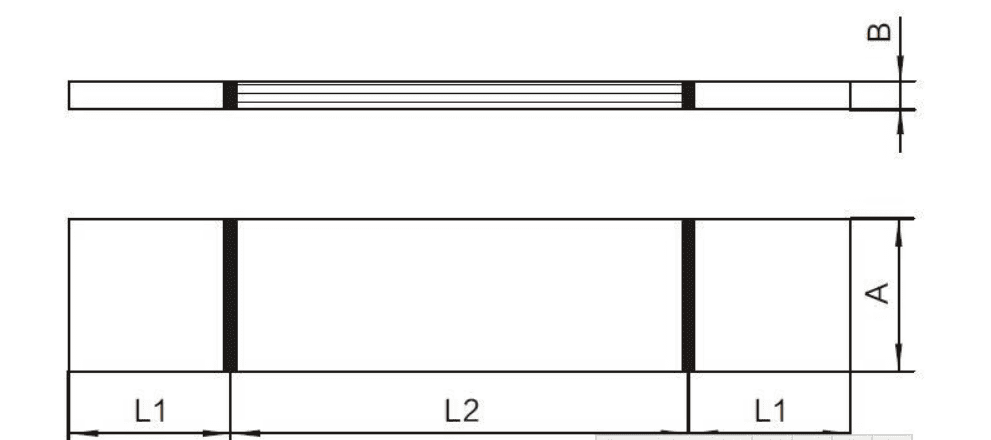
The data table of no plating flexible copper foil laminated connector
Catalog No. | Main dimensions(mm) | |||
A | L1 | L2 | B | |
MST – 4×40 | 40 | 60 | 170 | 4 |
MST – 5×50 | 50 | 70 | 170 | 5 |
MST – 6×60 | 60 | 80 | 190 | 6 |
MST – 6.3×63 | 63 | 80 | 190 | 6.3 |
MST – 6×80 | 80 | 90 | 190 | 6 |
MST – 8×80 | 80 | 90 | 190 | 8 |
MST – 10×80 | 80 | 90 | 190 | 10 |
MST – 8×100 | 100 | 115 | 220 | 8 |
MST – 10×100 | 100 | 115 | 220 | 10 |
MST – 10×120 | 120 | 140 | 220 | 10 |
MST – 10×125 | 125 | 140 | 220 | 10 |
MST – 12×120 | 120 | 140 | 220 | 12 |
MST – 12×125 | 125 | 140 | 220 | 12 |
MST – 12.5×125 | 125 | 140 | 220 | 12.5 |
Models | Specifications (thickness, width, overall length) | Copper Sheet | Copper foil | Copper Sheet |
MST | 5*50*290 | 60 | 170 | 60 |
MST | 6*60*340 | 75 | 190 | 75 |
MST | 10*60*340 | 75 | 190 | 75 |
MST | 6*80*380 | 95 | 190 | 95 |
MST | 8*80*380 | 95 | 190 | 95 |
MST | 10*80*380 | 95 | 190 | 95 |
MST | 8*100*450 | 115 | 220 | 115 |
MST | 10*100*450 | 115 | 220 | 115 |
MST | 10*120*450 | 140 | 220 | 140 |
MST | 10*125*500 | 140 | 220 | 140 |
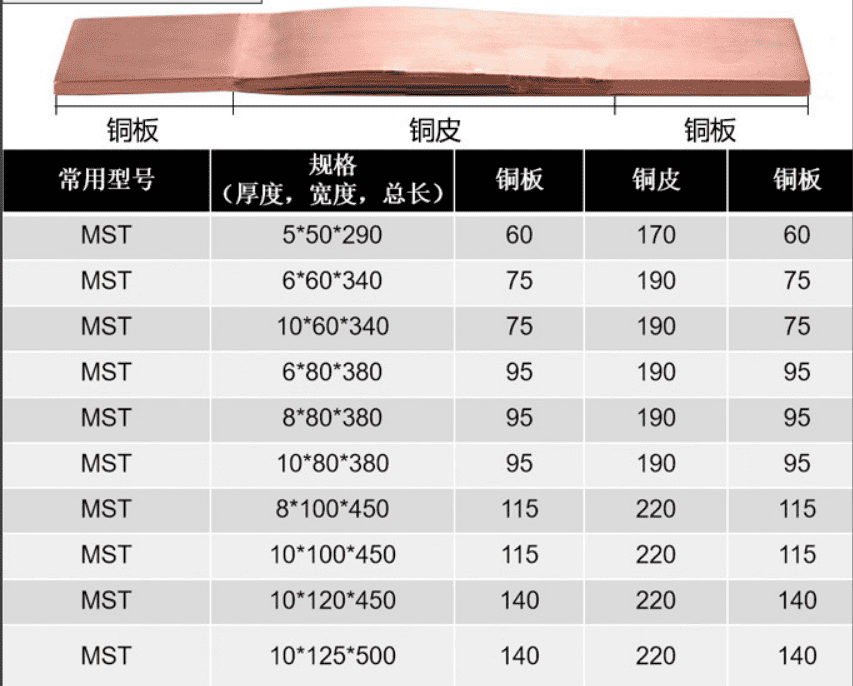
The data table of no plating flexible copper foil laminated connector
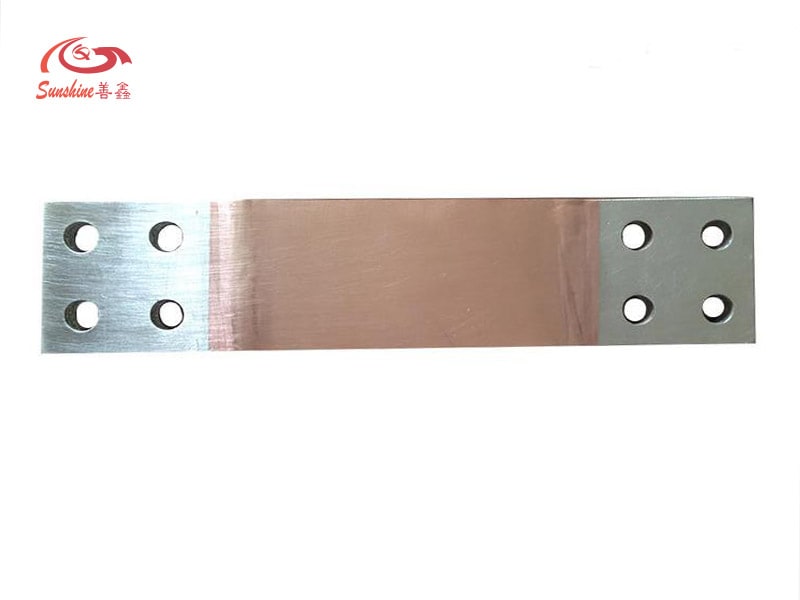
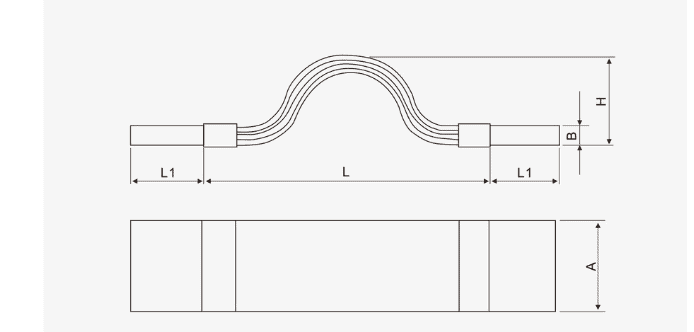
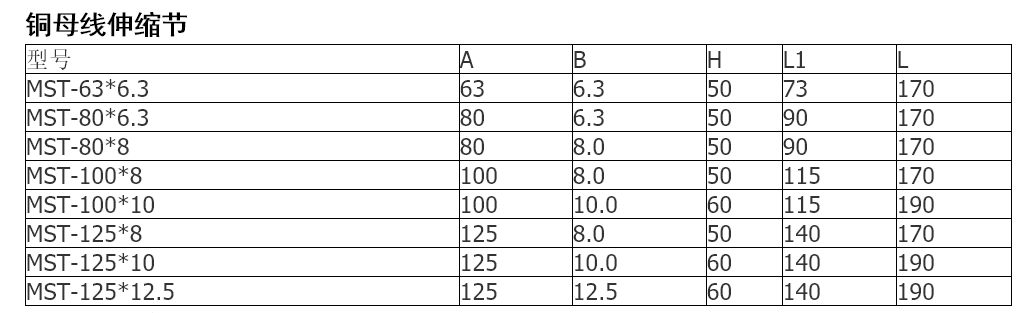
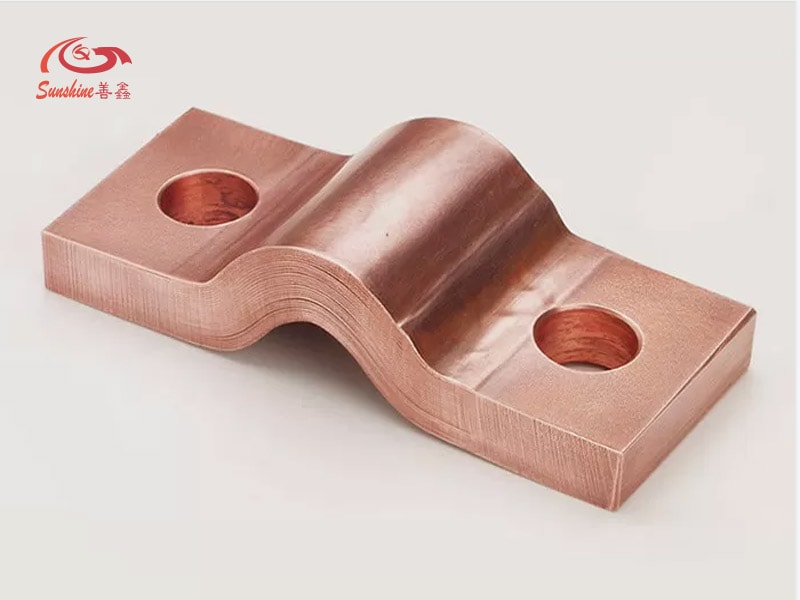
When you place an order, please specify:
- Length (L)×Width (W)×Thickness (T)
- Connector Shape & Hole Type
- Hole Diameter (d)
- Single Foil Thickness (default 0.10mm)
The application of flexible copper foil laminated connectors
The flexible copper foil laminated connectors are mainly used for high and low voltage electrical appliances, vacuum electrical appliances, high and low voltage switchgear, welding equipment, silicon rectifier equipment, cable bridge grounding, closing busbar trough, transformer device, car, electric locomotive, industrial furnace, mine explosion-proof electrical appliances, generator set, carbon brush wire soft connection and busbar connection.
The advantages of No plating flexible copper foil laminated connector
No plating flexible copper foil laminated connector is commonly used for industrial purposes as flexible expansion joints for connecting the bus bars in different applications.
They are made by stacking several foils of electrolytic copper which may be strips with riveted or welded contact areas. Once they are stacked together, they are applied high current and pressure.
- The surface area of the conductor is enlarged to increase the conductivity.
- Reduce stress damage to power supply facilities,prolong service life, and avoid maintenance.
- Adjust equipment installation error to improve installation efficiency.
- Good heat dissipation, auxiliary cooling effect.
- It can avoid the operation accidents caused by earthquake and displacement.
- It makes the conductive connection between high current equipment more convenient, reliable and safe, and protects the associated equipment from external force.
- Easy installation, high electrical rate, energy saving, low connection resistance, good electrical conductivity, strong anti fatigue ability, long service life and maintenance free.